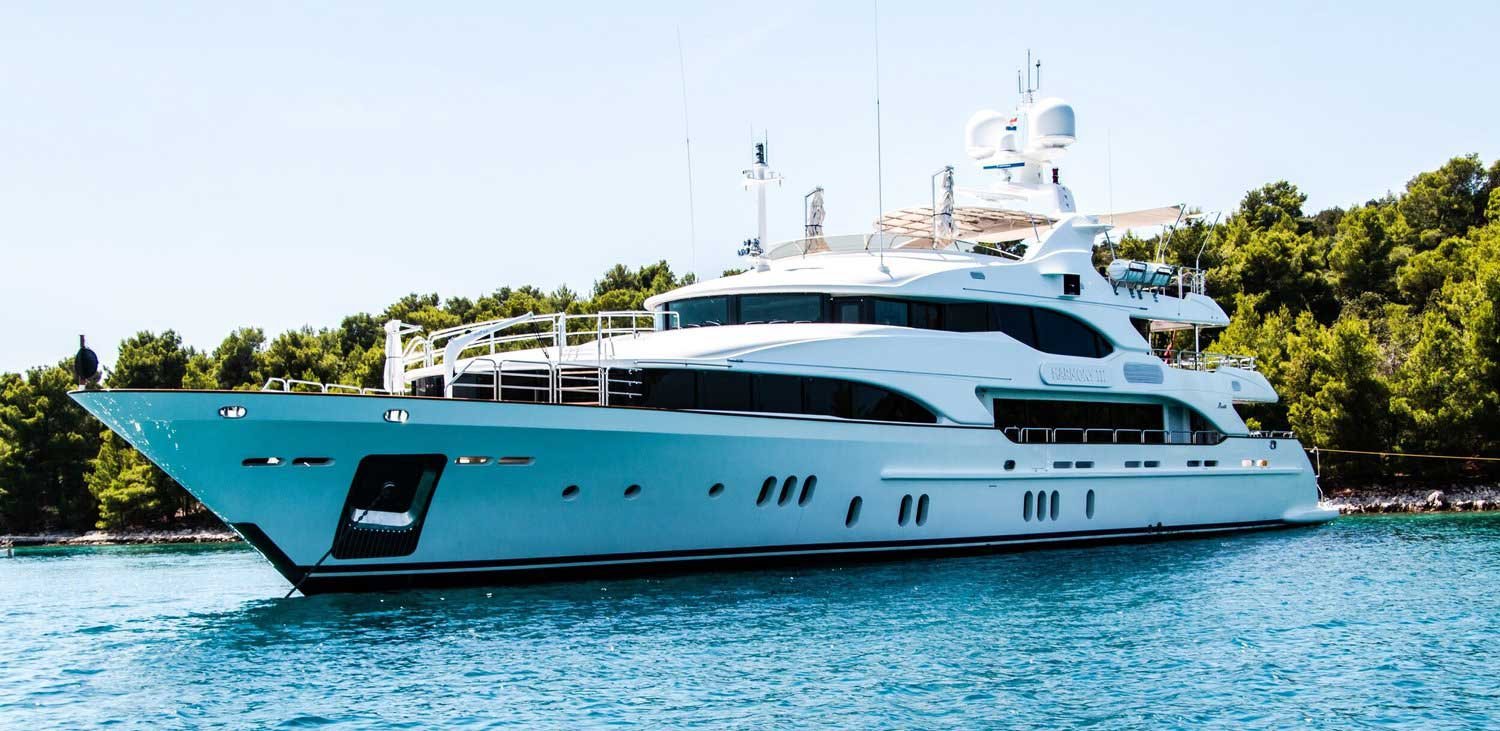
Welcome to Diecon Marine.
Confidence at Sea.
Quality. Durability. Reliability.
At Diecon Marine, we are proud to be synonymous with superior quality, long-lasting durability, and unmatched reliability.
We specialize in the design and manufacture of Diecon-branded Australian-made shell and tube heat exchangers. Leveraging our extensive engineering expertise and advanced manufacturing capabilities, we can replicate nearly any original heat exchanger component—particularly when OEM parts are obsolete or face extended lead times for import. This allows us to provide timely, high-quality alternatives that ensure your equipment operates at peak performance.
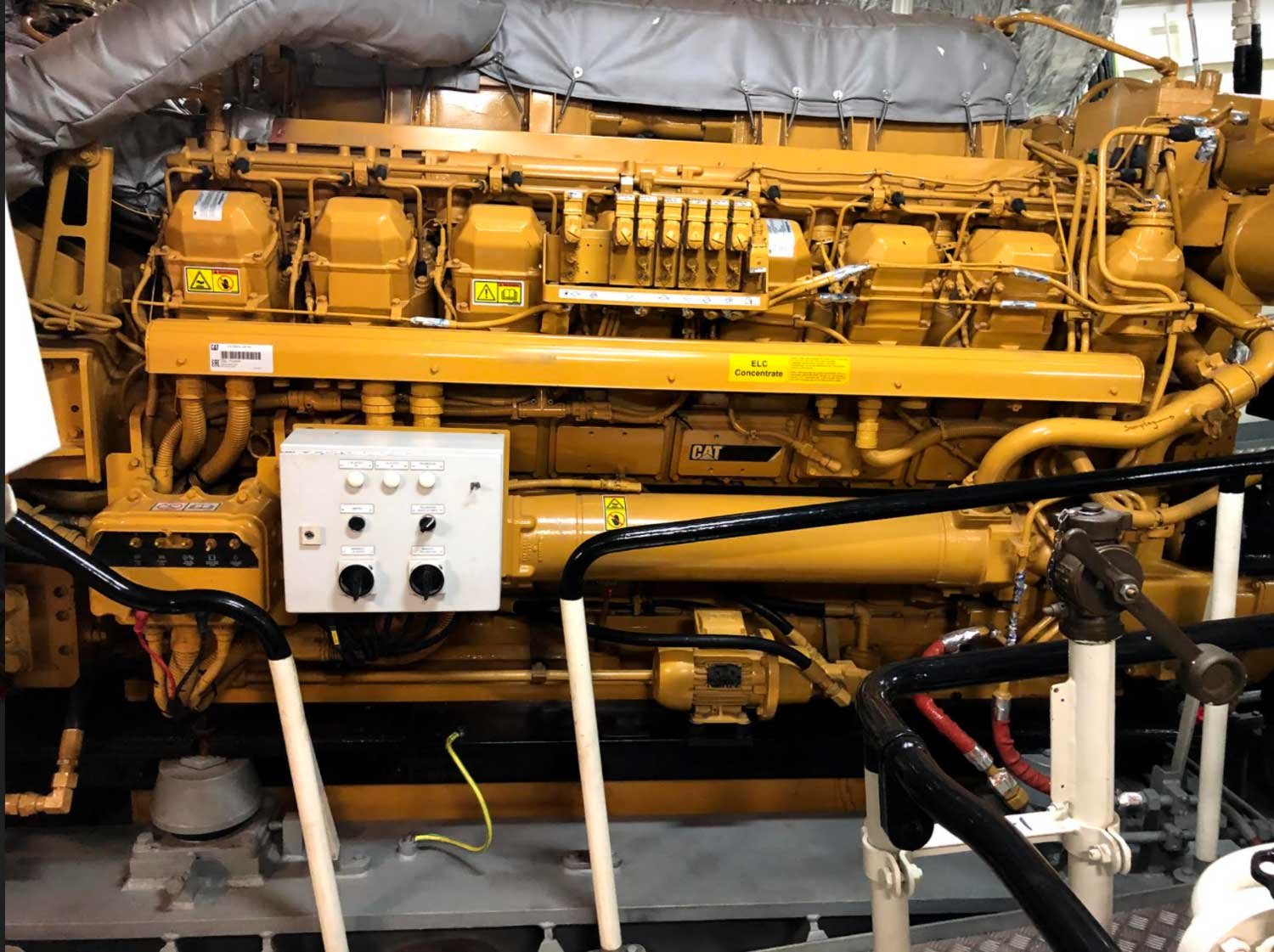
Experience Real Value
Our products are designed and manufactured to the highest standards, with safety, durability and reliability in mind.
The Diecon Difference
At Diecon Marine, our in-house engineering team specializes in designing superior, custom replacement solutions for a wide range of marine cooling components. This includes Shell/Tube and Shell/Plate Heat Exchangers, Keel Heat Exchangers, Water-Cooled Manifolds, Exhaust Mixers, and After Coolers (CACs), ensuring optimal performance in even the most demanding conditions.
Building on our core expertise, we are continuously expanding our capabilities. With ongoing investment in cutting-edge equipment and a relentless focus on innovation, we are now manufacturing an even broader range of high-quality marine equipment and components to meet evolving industry needs.
Our products are meticulously designed, developed, and manufactured to the highest standards of quality and precision, setting us apart in the industry.
As part of the RDM Group, we are proudly Australian owned and operated, with all manufacturing processes carried out locally in Australia. This commitment ensures that every product reflects our dedication to exceptional craftsmanship and local expertise.
Products by Diecon Marine
Case Studies
RiverCity Ferries
The fleet of 24 vessels were encountering overheating & performance issues with the exhaust manifold, along with difficulties in servicing, high costs, and downtime issues related to genuine Cummins heat exchangers.
Perkins Heat Exchanger
A customer approached Diecon Marine with a Perkins heat exchanger housing that had been poorly repaired by a local engineer. The existing housing needed to be replaced, but the client struggled to find a new housing or a provider capable of manufacturing one with a new tube bundle.